I am making good progress with the Beogram 6000 (Type 5505) from the UK. The initial assessment of this unit is posted here. This post discusses the restoration of the deck except the work on the CD-4 pre-amplifier, which will be the subject of a separate subsequent post.
This shows the Beogram as received with the panels and the platter removed:
As usual I started working on restoring the carriage. This shows the arm lowering mechanism comprised of yellow solenoid and bronze damper:
I removed all moving parts from the arm lowering section, the rods that guide the carriage, and the spindle that drives the carriage. Another part that needed to be extracted for cleaning and lubrication was the linkage that goes from damper to tonearm back. This requires the removal of the sensor arm. This shows the arm assembly taken out and the linkage removed:
Up front you can see the small copper pad that is glued to the sensor arm assembly to reduce friction between arm upper limit screw and the base of the arm. It always comes off if one tugs only slightly on it due to the degradation of the double sided tape that attaches it to the base of the arm. I usually glue it back into place with epoxy.
An inspection of the arm lowering components revealed an often found issue in this vintage Beogram 4002: A cracked solenoid arm lever extension:
This is a 'dangerous' issue, since the plastic extension has the task of activating the solenoid switch that reduces the current through the solenoid once it has lowered the arm. If it completely breaks off, the solenoid can overheat and the wire insulation of the windings burn off - usually the end of the solenoid, and it has to be rewound or replaced. I drilled out the rivets and removed the cracked plastic part. Then it was time to clean all the components in an ultrasonic bath. This shows the shiny parts after the clean:
I installed a 3D printed replacement extension on the solenoid lever
and put everything back together. Two things left to address on the carriage: The first one was to replace the original light bulb in the tracking sensor, which is situated in the black housing seen here:
I removed the bulb housing, which revealed the sensor aperture that is used to measure the arm deviation as it is pulled inward by the playing record:
After making sure that the aperture does not chafe with the sensor base, I installed the Beolover LED assembly. It has an integrated trimmer (blue) that allows adjusting the intensity of the LED light. This is very useful for fine-tuning the tracking feedback:
The final carriage task was to replace the cracked plastic pulley with a nice machined aluminum reproduction:
Now it was time to restore the AC platter motor and the motor and reservoir capacitor section. This shows the original setup:
I removed all components and cleaned the compartment:
Then I was time to take the AC motor apart for an oil infusion of the bearings. This shows the motor as extracted:
And here opened up - the simple design of this brushless synchronous motor delights me every time:
I immersed the enclosure in oil and pulled a vacuum:
While the infusion was going on I had a look at the power LED wiring and found this small circuit inside a plastic tube around the wire:
It consists of a resistor and a rectifying diode, which allows to hook up the added power LED directly to the AC secondary of the transformer.
After the oil infusion I put the motor back together using 3D printed brackets to replace the rivets that I had to drill out for opening it up. then I installed it together with a 3D printed assembly that holds the new capacitors in place:
Then I lifted the main PCB up for restoration:
This reveals the two power transistors of the push-pull driver of the AC platter motor. They are bolted to the bottom of the metal enclosure for heat dissipation. Someone already had replaced the original TIP 31/32 transistors with modern TIP41/42, so I left them in place:
While the board is up it is a good moment to replace the solenoid transistor, which was still the original TIP41A:
I replaced it with a new higher voltage type, a TIP41C:
It is rated to 100V, which hopefully will help it coping better with the EMF voltages generated when releasing the solenoid. At that point I also replaced the solenoid resistor (white 'box' in back) and the electrolytic capacitor on the board (orange):
This shows the modern components implanted:
On the main PCB I replaced the electrolytic capacitors, the RPM trimmers, the sensor arm amplifier, the H-bridge transistors and the driver for the push-pull stage of the AC motor. This shows the board after replacing the parts:
After this it was time to adjust the sensor arm amplifier bias with the 25 turn trimmer that I installed to get 4V at the collector of this transistor:
Once adjusted the trimmer has to be installed on the component side to not interfere with the closely spaced platter:
At this point I focused on replacing the remaining three incandescent bulbs in the deck. This shows the RPM panel removed with bulb compartments opened up:
I usually replace the bulbs with Beolover LED assemblies that solder directly to the bulb solder terminals:
This shows them installed in-lieu of the bulbs:
I tested the LED assemblies to verify that the white background reflectors under the RPM scales do not need replacement:
At least at the 33 RPM trimmer these backgrounds are often wavy due to the fairly high heat dissipation from the original bulbs, which softens and degrades the plastic strips that form the backgrounds. In the case of this Beogram 6000, the backgrounds were in perfect condition, a further indication that this deck was only used lightly, if at all.
The final bulb to replace was in the sensor compartment at the end of the sensor arm. This shows the original setup after pulling the compartment out:
The LED replacement assembly is shown next to the bulb compartment. This picture shows it installed:
And in action:
After replacing the sensor arm light source it is always a good idea to verify that a good sensor signal is achieved when there is no record on the platter. I hooked up the oscilloscope to the collector of the sensor transistor and spun the platter by hand. This is the strong signal I was able to measure:
More than enough amplitude! While the oscilloscope was fired up, I also measured and adjusted the motor voltage. This shows the sine wave that I measured for 45 RPM:
Then it was time to do a 24 hrs RPM stability measurement with the BeoloverRPM device:
The BeoloverRPM is able to log the RPM for long periods of time. This is the curve that I measured over 24hrs:
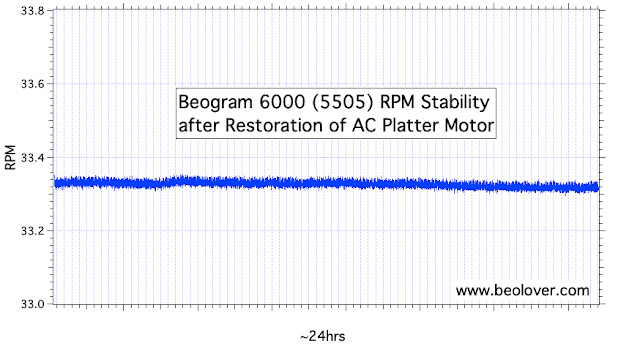
As usual, these curves are pretty uneventful for AC motor Beograms. The AC motors run very consistently due to their brushless synchronous motor design, and the high stability of the Wien oscillator that drives them. This platter drive was ready for prime time!
The final steps before giving this deck a tryout were calibrating the tracking weight, and doing all the adjustments to parallelize the arms, platter and floating sub-chassis. The picture below shows my approach to secure the tracking weigh in place: I replace the flimsy circlip that holds the counterweight adjustment screw in place with a M3 nut:
This makes sure that the calibration remains consistent, even during transport. Then I calibrated the scale on the small weight adjustment wheel to be acceptably accurate around 1.2g, the weight that most B&O cartridges prefer:
Next was the adjustment of the arm limits. This shows the lowering limit, which needs to be adjusted that the needle misses the platter ribs at the setdown positions:
This is a safety precaution in case the arm lowering circuit would ever malfunction and lower the needle on a rotating platter without record present.
Then I adjusted the tracking sensor feedback:
At this point the functional restoration was pretty much complete, except for the CD-4 output board. I thought it would be a good idea to try and see if the CD-4 pre-amp was working at all. So I put the first record Stanley Clarke (bassist of Return to Forever) headed himself in 1974 (
"Stanley Clarke", Nemperor Records NE431) on the platter and pressed START:
And, amazingly, the record sounded pretty good through the unrestored CD-4 pre-amp. A happy starting point for working on the CD-4 circuit, for sure! The restoration and exploration of the CD-4 board will be the subject of an upcoming post. Stay tuned!